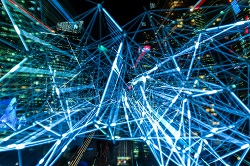
PCB的焊膏印刷是SMT生产工艺的重要环节,焊膏印刷质量直接影响最终的焊接质量,而5G超大尺寸PCB焊膏印刷更属于业界工艺难点。本文在介绍焊膏印刷工艺的基础上,采用鱼骨图分析影响焊膏印刷的各项因子,研究其中主要的影响因子对印刷的影响,实施针对性改善措施。研究表明,有效补偿钢网设计、提升印刷机精度、使用印刷底座和加强钢网及PCB表面清洁能够有效解决了超大尺寸PCB焊膏印刷问题,印刷直通率得到大幅度提升。 关键词:超大尺寸PCB;焊膏印刷;鱼骨图;印刷直通率 绪论 焊膏印刷工艺 表面贴装技术(Surface Mount Technology,SMT)是电子组装的核心工艺,其工艺优劣会直接影响产品的整体质量,而焊膏印刷工艺是整个SMT工艺流程中的关键工序之一。 当前,焊膏印刷工艺主流仍为丝网印刷模式。其流程为制作印刷钢片,通过印刷机将焊膏分配到所需PCB焊盘上,然后完成贴片和回流焊接。其中,丝网印刷原理如图1所示。 印刷工艺流程涉及影响因素众多,包括印刷机设备、钢片模板、刮刀、焊膏、PCB基板、印刷工艺参数和操作环境等。印刷机完成焊膏分配后,单板流入检测工位进行SPI检测,SPI检测对单板焊盘上的印锡量及印锡形状进行管控,合格的单板进行流出,对检测有缺陷的进行告警拦截,等待人工处理。完整的单板印刷工艺流程如图2所示。 图2 焊膏印刷工艺流程图 很多公司的经营理念都是实时消化库存,不想备库存。但目前来看,一些库存稍多的人在接下来的几个月里突然变得非常有前瞻性。因此,使人们开始重新审视他们如何看待这些事情。所以,我认为这些将是一些经验教训,“解决这类问题也许有不同的方式。” 超大尺寸PCB焊膏印刷难点分析 为保证信号传输质量,通常5G基础设备产品PCB设计尽可能集成设计,这样超大尺寸PCB已成为其选项。 相对于常规尺寸PCB,超大尺寸PCB(长宽满足700mm×400mm以上)焊膏印刷难点在于: 1)PCB厂加工公差造成PCB尺寸、器件焊盘位置、翘曲度等指标差异较大,导致钢网、印刷参数等出现极大不确定性; 2)由于采用了不同板材混压设计,加剧了变形风险; 3)受制于PCB厂加工位置精度,表面平整度,自重引起的下凹经过高温回流后,由于热胀效应,PCB会出现不同程度形变、弯曲,钢网设计难度加大,对钢网下锡性提出更高要求; 4)单块PCB上超过2万个器件,涉及不同封装,各器件对焊膏需求的量参差不齐; 5)业界普通型号印刷机由于PCB尺寸超过上限,无法满足印刷要求,其对焦精度、重复印刷稳定性提出了更高的要求; 6)底部支撑普通顶针无法满足支撑要求,需要制作专业印刷底座,满足支撑需求; 7)生产环境,外界容易引入污染,对清洁提出了更高的要求。 焊膏印刷影响因子分析 根据5G超大尺寸PCB印刷质量要求,采用了鱼骨图对超大尺寸PCB的印刷影响进行全因子分析,找出主因。针对每一个主因进行专项改善。超大尺寸PCB印刷影响因子鱼骨图如图3所示。 图3 焊膏印刷影响因子鱼骨图 根据PFMEA确定关键因子(过程略),确定重点研究钢网设计、印刷机精度、印刷支撑系统和环境清洁方面对PCB焊膏印刷结果的影响。 钢网设计与制造的影响研究 钢网影响焊膏印刷主要为焊膏的印刷释放率。焊膏印刷释放率定义为:释放到焊盘上的焊膏体积和钢网开孔体积之比。钢网设计中最重要的控制参数为开孔尺寸和模板厚度,因为开孔尺寸和钢网厚度将直接影响焊膏释放率。 影响焊膏释放率的其它因素有:钢网开孔孔壁的几何形状、钢网开孔孔壁的光滑程度、钢网和PCB板的分离速度、钢网和PCB板的间隙、钢网开孔尺寸的精度以及焊膏的粘度等因素。 钢网的面积比为垂直钢网的面积和侧壁面积的比值,宽厚比为开孔宽度和钢网厚度的比值。钢网开孔如图4所示。 图 4 钢网开口示意图 面积比=开孔面积/开孔壁面积= ( L × W) /[2 × ( L + W)× T],宽厚比=开孔宽度/钢网厚度=W/T。L为钢网开口长度,W为钢网开口宽度,T为钢网厚度。为保证钢网印刷不少于75%的焊膏释放率,必须要使宽厚比>1.5,面积比≥0.66。 钢网制造方式对钢网的侧壁光滑程度、精度等也具有重要影响。目前钢网制造方式有:化学蚀刻、激光切割和电铸成形三种,其性能参照表1所示。前两种属于减成工艺,最后一种属于加成工艺。目前在实际生产中,考虑成本和交货周期因素,主要采用激光切割方式,特别是有密脚间距器件的钢网生产。 表1 不同钢网制作工艺对比 超大尺寸PCB由于自身材质原因,经过高温回流后,会引起不同程度的形变翘曲,实际印刷生产TOP面时左边部分往左偏移,右边部分往右偏移,无法通过现场调试来解决。制作钢网时需根据完成BOTTOM面焊接的实物考虑,而不是根据CAD图层进行制作,需要进行一定距离补偿,以免焊盘位置和钢网开口位置不匹配,导致印刷产生偏移。 本文随机选取2个生产批次,且完成BOTTOM面生产后的实物单板,进行三次元测量,研究大尺寸单板的缩胀规律总结数据,统计数据如表2所示。 表2 缩涨变化情况 另外,普通材质钢片下锡性较差,制作FG材质并进行纳米涂覆,孔壁残留明显减少,有效增强焊膏下锡性,印刷漏印、少锡等不良明显减少。选取3个批次进行印刷效果对比,结果如表3所示: 表3 批次变化情况 印刷参数影响 全自动焊膏印刷机的对位过程是指视觉系统根据PCB和钢网上的两个Mark点的坐标值偏差,结合相应的对位算法求解纠偏量,通过平台的横向、纵向及角度的精细调整,使PCB的Mark与钢网的Mark完全重合。 超大尺寸印刷机,对位精度控制更加困难,针对超大尺寸PCB的印刷,在整体的结构上,改良了抗震性、高强度一体成型的主体框架结构,机体材料处理的工艺包括熔接→热处理→退火→基准面切屑抛光处理等,使得整体机体结构不会扭曲变形,为后续精准、稳定的印刷品质,提供可靠的基础。 良好的机器整机性能很重要,每次印刷校正补偿机构都可以完成精确钢网与PCB精确对位。印刷机的精度控制,并不是某一个控制单元的精度控制,而是一个各个运动单元以及各个控制系统的相互协同输出的一个综合性精度控制。机器零部件的制造,存在零部件的制造精度、组装过程中存在的装配精度以及完成组装后的整机测试精度,都需要使用科学的方法进行测量与评估,来降低机器本体属性所带来印刷缺陷的风险。随着5G应用推广,PCB单板印刷尺寸逐步扩大,密脚芯片引入,对印刷工艺提出新的要求,新的挑战,超大板印刷与印刷精度控制研究很有现实意义。 印刷支撑系统的影响 印刷支撑为PCB焊膏印刷工程中关键因子,能否获得良好的印刷效果与支撑直接相关。印刷机常用支撑有3类,分别是真空软顶针、硬顶针、印锡底座。三种支撑形式各有优劣。真空软顶针可有效避免撞件,操作简单,但会出现支撑力度不足的致命缺陷;硬顶针是印刷机厂家配置的,其优点是可以根据需要布放,支撑力足,可以获得较好的撑着效果,其缺点是对技术员要求较高,放置不当容易撞件发生批量质量事故;印锡底座为近年来流行的支撑方式,其优点是一体化成型,对技术员要求降低,也可获得较好的支撑效果,取放方便,缺点是特定性,单板需要定制专用的印锡底座,通用性很差,且有批量撞件风险。 PCB翘曲直接影响印刷过程中是否得到了良好的支撑,进而影响印刷质量。日本学者田中和吉就PCB翘曲而产生应力的过程做了如图5所示的描述:当三根以上的引线成一条直线被固定在PCB上时,如果在此a1的翘曲,则被引线固定的间距S2内的PCB翘曲就会被矫正至a2,此时引脚承受的负荷分别为W1和W2。 可将其作为连续梁来处理,当忽略引线的变形时,可用力矩分布法来求负载,如下公式所示: W=δEt³da2/S2² 式中,W为引线内部产生的负荷 δ为系数 E为PCB的杨氏模量 t为PCB厚度 d为引线占有的PCB宽度 S2为端子排中最外侧两根引线的间距 a2为间距为S2所对应的翘曲量 翘曲原理:FR-4由芳香族环氧树脂、硬化剂、阻燃剂、玻璃织物和各种添加剂组成。虽然一般环氧聚合物的热膨胀系数CTE在70~90 ppm/℃,可是玻璃纤维的加入限制了热膨胀形变。理想的CTE应该和Cu接近,大约是18 ppm/℃。低热膨胀系数的FR-4可以减轻弯曲问题,同时也使组装后元器件所受的应力减小。 玻璃化转变温度(Tg)是PCB基材层压的一个经常用到的判据。Tg指的是聚合物中发生相变的温度,当几种树脂混合在一起时它不一定是一个精确的常数值。聚合物在低于玻璃化温度时处于一种更刚性的类似于玻璃质的状态,这时它具有高强度和低CTE。温度超过Tg时,可以使材料转换成一种橡胶态,聚合物变软,热膨胀率也会加大。来料板材是一个经过高温高压的过程,在压制过程中会残留不同的应力,即使同一规格基材不同批次之间的尺寸一致性也较差。 超大尺寸PCB来料主要来自不同PCB供应商,不同供应商的制造工艺能力有差异,再加上大尺寸PCB工艺流程更加复杂,加工难度增加,误差就会加大。经过回流后仍会出现不同程度形变,对印刷支撑的要求更加严格。大尺寸PCB板印刷过程中对支撑方面要求较高,使用真空软顶针的支撑方式无法满足支撑要求,进而引起连锡、少锡等印锡不良现象,对此,需要特别制作专用印锡底座,来解决支撑问题,单板专用制程底座。 钢网及PCB表面洁净度的影响研究 钢网和PCB表面存在异物,很容易导致印刷出现短路、偏移等不良,出现这类不良只能进行二次印刷,印刷质量风险增加。 日常生产过程中,钢网清洗要求钢网每隔12小时进行钢网清洗。由SMT生产操作员将钢网送到钢网清洗房,由钢网清洗房设备操作员统一用清洗机自动清洗。一般清洗过程中,清洗完成后肉眼检查无任何异物及焊膏残留,则将钢网装回印刷机上,添加焊膏,进行印刷生产。 PCB清洁动作主要包含两个方面。一是上板清洁,PCB上板时,SMT操作员手持清洁滚轮对PCB进行表面全覆盖的2~3次清洁,去除PCB表面灰尘和污物,确保PCB印刷面的清洁度;二是PCB的清洗作业,当PCB贴片紊乱或者大面积印锡不良时,需对PCB进行清洗作业,一般是先刮除表面物料和焊膏,再清洗干净重新印刷。 在大板的生产过程中,为了保证印刷质量,减少因钢网残留异物、堵孔等导致的洗板重印动作,过程清洗钢网时加入电子放大镜检查,避免清洗不彻底的钢网上线。 超大尺寸PCB板在印锡工序中,异物残留导致SPI报警占的比率很大,针对于此,增加了清洁除尘工序及使用手电筒、放大镜等检查工具检查包括PCB来料、生产过程等环节残留的异物。 改进成效 为保证5G产品PCBA贴片质量,本课题选取了某款超大PCB作为研究验证对象,经过团队技术攻关,分析技术难点实施针对性闭环改善措施,做好过程质量管控,及时对后端检测发现问题实行针对性有效闭环,超大尺寸大板印刷问题得以有效改善。统计该单板的印锡SPI设备检测合格率月平均值。单板印刷检测合格率在6个月内提升了24.2%。验证措施有效,问题得到闭环解决,超大尺寸PCB印刷合格率得以稳步提升。 结论 超大尺寸PCB作为当前SMT设备加工能力极限,大板与钢网加工公差叠加导致焊膏印刷问题给生产带来极大的挑战,一直是业界难点、痛点。本研究结合5G产品的设计需求,从实际单板的闭环改善出发,立足于印刷的现实问题的改善,优先验证了措施的有效性,对超大尺寸单板的印刷问题解决具有一定的参考价值。论文得出以下结论: PCB设计为保证信号完整性而采取不同板材混压设计、低损耗设计、非对称设计等增加了PCB加工的公差精度、翘曲、残余应力、残铜非对称等风险。 多厂家、多批次PCB制造带来的位置精度差的问题可通过钢网开口的坐标补偿来降低,在材质上涂纳米涂层的FG材质钢网的下锡性优越。 印刷机单轴运动精度、平台水平度以及各平台之间的平行度、重复印刷精度三个方面的精度有效保障了超大尺寸单板印刷精度。 设计专用的印锡底座能够有效的应对超大尺寸单板支撑不足的问题,对于实际的印刷改善很有必要。 减少或消除外界带来的钢网以及PCB表面污染是印刷合格率提升的有力保障。