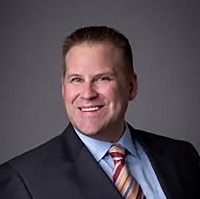
工业4.0简述
大数据是工业4.0的基础,因此先进的检测系统必须从简单的 “合格/不合格”判定工具发展为高度直观、动态的决策系统,尤其突出的是对可靠、可追溯数据的需求。人工智能(AI)引擎可以通过管理焊膏检测(SPI)和自动光学检测(AOI)系统的制程数据来帮助客户分析和优化生产制程。
从光学检测市场的增长轨迹来看,制程挑战有助于创新。例如,用于收集焊膏沉积图像的2D检测技术无法解决阴影问题,焊膏检测(solder paste inspection ,简称SPI)从2D发展为3D,因此制造商开发了3D SPI来获取印刷的焊膏高度的信息,以准确测量所印刷焊膏的总体积。几年后,我们发现采用AOI系统检测表面贴装元器件时也有同样的需求。
随着电路板上元器件和焊点越来越多、密度越来越高以及封装器件越来越小,例如0201公制(008004英制)微芯片(图1),目前的电路板复杂性在不断增加,因此采用Blob分析或高像素摄像头的AOI技术已不再可行。做出的大多数决策都是基于与基准图像“好/坏”的比较,很容易受到诸如元器件表面涂层、电路板状况、元器件接近度等变量的影响。
图1:以圆珠笔为基准,对0201公制(008004英制)元器件、0402公制(01005英制)元器件及0603公制(0201英制)元器件进行比较(来源:ASM Assembly Systems GmbH)
尽管2D AOI仍然是目前还在使用的一项技术,但更多的制造商正在采用3D AOI来提高电路板质量。3D AOI的优势显而易见,使用由准确数据支持的界定清晰的阈值,将无需持续调试检测程序。此外,通过一些3D AOI生成的测量数据可深入分析制程,有助于消除缺陷的根本原因。将3D SPI与3D AOI结合使用可使制造商能够准确地控制和监视电路板组装制程。
但是,由于数据量太大,工程师很难采用传统技术和软件来进行收集、处理和利用所有数据。AI和深度学习为机器通过大量的工艺数据进行学习提供了基础,这些机器可根据数据输入来调整输出,帮助工程师更智能地完成任务。许多我们听说过的实例,例如会下棋的计算机或自动驾驶汽车,都是通过处理大量数据并识别数据中的图形进行深度学习来完成任务。
这对于PCB批量生产和帮助智能工厂创建数据集是非常理想的。基于人工智能的平台可以智能地应用实时数据来改善生产制程,包括统计过程控制到实时程序完善。除了智能工厂解决方案之外,制造商还可以采用相同的技术通过执行复杂的机器学习算法来优化制程并调整制程参数。
实现智能工厂就是在检测区域提高生产率的同时对制程和系统采取切实可行的方法。将机器学习与检测期间生成的3D测量数据相结合,可帮助制造商明确界定低效率并提高生产线效率。机器学习采用收集和分析输入数据的编程算法来预测可接受范围内的输出值。再将新数据反馈给这些算法,他们可学习优化其操作以提高性能,并随着时间的推移提高智能度。
例如,某些工具允许制造商同时调用程序及检测多条生产线的状况,从而提高生产率,更重要的是实现了具有一致性能的数据完整性。操作员可以使用其他实时监控工具进一步改进生产线维护,可以远程显示相关制程参数,实时进行分析和采取措施。此外,将SPI、再流焊前AOI和回流焊后AOI的多点视图,与实际数据管理和监视结合起来,使操作员依此做出可行的决策来优化流程。同时基于AI的制程工具可使优化达到更高级别。
转换所有数据需要使用仿真工具利用印制电路板组装(PCBA)生产线积累的历史数据来审查已识别的缺陷,同时避免不必要的停机。软件工具可以使制造商在不停生产线的情况下可靠地预测调整效果。未来AI驱动平台可自动把复杂的制程优化决策提供给专门的制程工程师。包含连通性即可创建智能工厂,例如,软件模块可以执行复杂的算法来给出闭环制程建议,机器与机器的连通性可通过实现自动SMT生产线维护,推动智能工厂向前发展。最终可将检测与丝印机和贴装机相结合,使网络工具能够连接并简化整个PCBA生产线的通讯。
由于需要确定影响制程的各种环境因素,所以定义正确的制程参数通常需要很强的专业知识。利用基于AI系统和M2M连通性,制造商可以将在线检测系统同生产线中的相关印刷机和贴装机连接起来,解决问题。图5显示了自动化机器学习如何与制程专家的想法相匹配,结果将会不断改进。
先进的过程控制方法
可靠的AOI方法已成为传统测试策略可行的补充。AOI可成功地用作测量印刷、贴装和回流焊性能的过程监视工具。其优点包括:
- 在过程监控期间检测和纠正SMT缺陷的成本要比最后检测的成本低,后者的维修成本通常是前者的5倍到10倍
- 尽早发现整个过程中的不良趋势,例如贴装漂移或不正确的贴装,如果不及早检测出,在功能测试和最终检测中就会发现具有相同缺陷的电路板
- 在回流焊前对元器件贴装进行验证,在组装过程中较早地识别出元器件缺失、偏斜或错放的元器件
然而,单个检测系统具有局限性,尤其是当与生产线其他设备通信受限或没有通信时。在这种设置下,根本无法优化PCBA制程。设备供应商必须合作沟通以实现零缺陷。M2M可以通过与生产线中的其他设备交换实时SPI和AOI测量数据来优化制程,这种实时反馈包括测量数据(例如偏移、体积、高度、面积和对其他系统的警告),同时分析趋势优化制程并识别趋势。连接的系统可以自动定义制程之间的关联。
例如,PCBA行业有许多研究和文档,详细介绍了回流焊工艺如何能够将表面贴装元器件正常地定位在焊盘上,即使元器件的放置有偏移。而且,将元器件的凸缘缩小至0.3mm或0201微芯片的趋势要求行业探索流程控制如何能够提升高密度贴装的良率。
先进的过程控制(advanced process control ,简称APC)是一种经过验证的控制和优化技术,可实现可测量及生产良率的可持续提高。大多数工程师都认为,稳定控制闭环、利用不足或无效的制程时间和紧密的制程交互是非常困难的。APC已成为实现稳定过程控制的标准解决方案,并且很简单,它是对过程自动化系统增值的升级。APC收集并分析检测系统的焊料和元器件位置数据,然后将意见通过生产线发送到丝印机或贴装机,实现自动闭环反馈(图2)。
图2:在焊膏丝印机、锡膏检测(SPI)、元器件贴装机和AOI系统之间采用APC主动反馈的理论SMT生产线
制造商希望通过随时随地访问所有数据来监视和调整流程,以实现零缺陷。他们还必须应对较短的生命周期,因此检查解决方案应该能够收集和分析大量数据以产生可追溯的结果。
APC丝印机反馈结果
对更小、更轻、更智能电子设备的持续需求导致越来越多地使用更小的元器件,这些缩小的封装导致了较小的开孔设计和更精细的焊膏,这使钢板丝印成为了高度复杂的工艺,对生产良率产生了巨大影响。据报道,所有PCB组装缺陷中有70%与焊料丝印工艺直接相关,制造商必须确保在生产过程中始终采用一致的最佳丝印参数。
由互连软件模块组成的改进解决方案可以通过将实时丝印信息与SPI测量数据相结合来主动优化丝印工艺。更高级软件可自动执行实验设计(DOE),以使用高级诊断算法和噪声过滤模型完成详细的SPI结果分析,然后推荐理想的丝印参数。该软件触发SPI将信息发送到丝印机,以自动调整参数。调整丝印机参数时,可以设置印刷压力、印刷速度和钢板分离速度的最大值和最小值。
其他软件可以使用多种异常检测算法来主动优化丝印工艺,并进一步减少误报。理想情况下,该软件将演变为自主生成优化模型,并采用实际结果调整工艺参数。虽然每个软件模块都可实现独立的工艺优势,但基于AI的综合软件功能将确保最高的制程可靠性和生产灵活性,而无需专用资源和专业知识。
APC贴装机反馈结果
利用丝印机与SPI设备通信有很多优势,那么贴装机和AOI呢? 将贴装机与AOI相连也可带来明显的好处,例如尤其是提升了高密度板的良率。贴装机使用收到的数据更新 贴装程序,确保将元器件放置在焊料沉积上,而不是放置在基板焊盘上。这种将元器件放置在印刷焊料上的方法利用自对准原理来提高良率并减少缺陷。如图3所示,当焊料偏离焊盘且将元件贴装到程序中预定义的贴装位置时,自对准是无效的。回流焊期间,元器件会偏移出焊盘或与其他焊盘桥接,导致返工或报废。
图3:过去回流焊之前和之后是将芯片放置在焊盘上(来源:North America-Process Automation公司Panasonic System Solutions Company分公司或PSSNA-PA)
相反,校正后的贴装将最大化利用自对准原理。将这些微芯片放在焊膏上而不是焊盘上,从而提高了良率和质量。图4显示了一组测试结果,通过这种高级通信,3D AOI可以将正确的贴装位置值提供给贴装机,确保贴装机将元器件放置在正确的位置。通过自动调整贴装位置并识别趋势以进行进一步的位置校正,可以提高制程的可重复性。
图4:在回流焊前后控制片式元器件放在焊料上的位置(来源: North America-Process Automation公司Panasonic System Solutions Company分公司或PSSNA-PA)
某些3D自动光学检测(AOI)系统采用定量测量的实时数据,将正确的元器件位置值提供给元器件贴装机,并确保将元器件安装在目标位置。这类功能可通过自动将元器件的位置调整到焊膏而不是焊盘位置来提高制程的可重复性(图5)。此外,该软件将采用AOI系统的真实3D测量数据来识别偏移趋势并进一步校正位置。
图5:回流焊前3D检测检查到零件偏斜的实例,检测结果将会反馈给贴装机
将检测系统与贴装机连接起来可帮助实现整条生产线的通信,进一步提高检测流程的价值。例如,M2M连通性可通过在丝印机、SPI、贴装机和AOI系统之间交换实时测量数据来优化制程。这些系统将偏移量和警告数据提供给其他系统,同时分析趋势以优化制程和可追溯性。经过优化的制程可实现卓越的性能。
设备之间的通信通过自动将元器件的位置调整到焊料沉积位置而不是焊盘位置来提高制程可重复性,这种先进的制程进一步提高了片式元器安装的可靠性。在智能工厂中,允许对实时结果进行关联、计算和可视化的联网智能系统将变得更加重要。
结论
工业4.0及其相关优势将有助于推动行业发展。设备供应商需要努力工作,加快实现M2M通信标准的实施将有助于推行工业4.0。IPC工厂数据交互(CFX)和IPC-Hermes-9852等标准为行业开发标准和创建智能工厂奠定了基础。这些M2M通讯标准,某种程度上由工业4.0引导,正在通过应用自动制程调整来提高首次良率和产量等指标,以迅速改进制造过程。通过与供应商的双向通信,不仅可以自动进行生产线转换,还可以使设备自动调整生产参数,从而通过消除返工和废品来提高电路板质量和降低成本。作为此任务的一部分,带有互连PCBA设备的APC将彻底改变工艺制程,并为智能工厂的发展奠定基础。
Brent Fischthal担任 Koh Young America公司美洲市场高级营销经理。