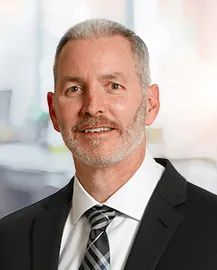
Patrick Valentine
Uyemura USA公司技术和精益六西格玛经理。Patrick的工作职责包括教授精益六西格玛绿带课程和黑带课程。Patrick获得了新英格兰商业和金融学院质量体系管理博士学位,拥有亚利桑那州立大学颁发的六西格玛大师黑带证书,也是一名通过ASQ认证的六西格玛黑带和可靠性工程师。如需联系可发邮件至pvalentine@uyemura.com。
简介
质量及持续改进是电子行业生产过程中必不可少的环节。因质量不良而付出的补救成本会占到一家公司年销售额的25%。追求质量和高可靠性是当今时代持续改进的推动力。
质量简史
对质量的控制以及减少产品变化可以追溯到公元前。公元前2100年的中国,夏朝已在使用早期的质量控制方法[1]。13世纪90年代末期,在中世纪的欧洲,同业公会(即工会的初期形式)负责控制产品和服务的质量[2]。从1700年到1900年,控制产品质量靠的是手艺人的工匠精神[3]。19世纪末期,Eli Whitney发明了标准化且可互换的部件来简化组装[3]。1875年,Frederick W. Taylor发明了科学管理原理,将工作细化成了更容易完成的小任务[3]。在Taylor看来,保障生产力及提高质量的关键在于知识、组织和领导力。1903年,Karol Adamiecki发明了协调图,这种图可以记录工人的移动和动作,显示导致生产效率低下、潜在质量问题的原因[4]。在20世纪初,由于制造商从之前单纯地关注生产成本转向了另一个目标——在产品数量保持平衡的同时还要满足客户对质量日益增加的需求,助推了质量原理的发展。
1901年,工程标准委员会(Engineering Standards Committee)在英国成立,该组织致力于为各个领域制定英国统一标准[3]。1906年,国际电工委员会(International Electro-Technical Committee)成立,为所有电气、电子及相关技术领域制定并发布国际标准。截至1930年,大多数工业化国家都成立了国家标准组织。其中大部分国家标准组织都加入了1926~1928年之间成立的国家标准化组织国际联盟。但是在20世纪30年代大萧条时期,全球标准化进程停滞不前,随着1939年第二次世界大战的开始而进一步受阻。
1941年,美国参加第二次世界大战。美国政府颁布法令要从民用经济转为军事生产。其间,通常只有那些要价最低的军火制造商才能中标。产品交付后才能检验产品质量,但这种质检方式会消耗大量的人力资源,并且会引起人员招聘和人才流失问题。在贝尔实验室和Walter Shewhart博士的帮助下,美国军方采用了样本抽查方法来节省资源成本和时间成本[2,3]。
1945年第二次世界大战结束后,全球质量标准进入了复兴时期,并在接下来的70多年里一直飞速发展。1946~1947年的这段时间非常关键,因为美国质量管理协会(American Society for Quality Control ,简称ASQC)和国际标准化组织(ISO)成立。质量管理标准开始专注于为客户提供产品价值、提高产品质量,以及加快生产速度和了解利益相关方经济活动所产生的影响。
20世纪60年代,人们对质量控制的思维模式发生了变化,变成了要在问题出现之前就发现潜在的风险。之后20世纪80年代,人们的思维模式又发生了一次转变,变成要在产品开发期间就关注客户对质量提出的需求。在很多行业内,设计实验和统计质量方法成为主流。精益制造理念也在日本以外的国家得到了认可。20世纪80年代期间,摩托罗拉发起了六西格玛项目,美国国会设立了Malcolm Baldridge国家质量大奖奖项, ISO发布了第一份质量体系标准。在接下来的十年间,精益原则从制造领域传到了服务组织。1998年,美国质量管理协会改名为美国质量协会(American Society for Quality ,简称ASQ),此举是为了给更多行业提供更好的服务。进入21世纪后的十年里,ISO发布了全球质量标准——ISO 9001:2000和ISO 9001:2008。2015年,ISO发布了第五版ISO 9001:2015《质量管理体系》。随后发布了ISO 13053-1:2011、ISO 18404:2015和其他涵盖精益六西格玛的标准。人们因质量不良付出的巨大代价,对可靠产品及安全性的需求,再加之全球范围内产品的全球化形势,都成为了统一质量标准运动的推动力。
因质量不良付出的代价
因质量不良付出的成本,就是因为不能首次就生产或提供完美的产品或服务而导致的所有成本,包括报废、返工、重购原材料、人工和库存等成本[5]。在3西格玛质量等级上运营的公司会支出年销售额25%左右的资金来弥补因质量不良问题而导致的成本[6]。其他公司这一比例在25%~40%[7]。质量不良导致的问题甚至可能摧毁一家公司。
意料外的产品失效(可靠性差)会大幅增加销售成本、一般费用和行政成本(SG&A),并且需要额外的库存和固定资产才能支撑运营。这些间接成本对利润的损耗比保修索赔流程导致的直接成本要多得多。产品召回会影响公司财务状况和公众形象。
印制电路板组件(Printed circuit board assemblies ,简称PCBA)变得越来越复杂,人们为减少“未发现故障”的失效情况(“no-fault-found” failures ,NFF),对质量和可靠性的要求不断增加。未发现故障的失效情况发生于产品使用期间,但后续检查分析时却找不出故障。随着PCBA变得越来越复杂,多重失效模式也越来越多,NFF范例也在不断增加。每种失效模式可能由几十种潜在制造缺陷导致的诱因造成。
航空应用对质量和可靠性的要求非常高。在众多对质量有高要求的领域中,航空航天业只是其中之一。医疗行业对质量和可靠性也有着类似的高要求。FDA列出了无数医疗产品召回案例和PCBA故障导致的质量问题案例。成百上千种缺陷会影响PCB和PCBA的质量[8,9]。业界正在开展持续改进项目以提高PCBA的质量和可靠性。
持续改进
持续改进=持续变化。如果一家企业想要进步,一定要有接纳变化的企业文化。难点就在于如何去明确和评估组织文化。组织文化可能是模糊不清且难以量化的,它是一种包含了组织理念、传统、共同期许、职业道德及企业价值观的共有信念体系,整个公司都应共同坚守组织文化。
不论是想怎样改进公司,一定要在流程中发现并确定问题;设计并管理一系列简单有效的数据收集方式、分析数据、确定待办事项、上报管理层,并且持续改进。优化后的持续改进文化可以利用领导层/管理层、创新精神、3S思考法和人力资源。
领导层和管理层对企业的成功与否起着决定性作用。领导层和管理层有着各自具体的职责,但也有组织共性(图1)。管理层关注的是运营卓越,通过影响人力资源的行动来优化运营。使用的方法包括实现短期目标、提高可靠性和效率、规避风险和持续改进。领导层关注的是创新,通过影响组织发展方向来促进创新。使用的方法包括前瞻性的领导力、再思考、重新进行工程设计以及改变管理层。组织既需要领导层也需要管理层。没有配备管理层的领导层是平庸的,而没有领导层的管理层是灾难性的。
图1:领导层和管理层
创新需要磨合、敏捷性和坚定的决心[10]。磨合指的是在不断讨论(甚至是非常激烈的讨论)过程中碰撞出有创意的理念。磨合的过程就是把团队的多样性和冲突都融合在一起,从而提出最佳的理念。敏捷性指的是团队利用发现式学习法来验证创意是否有效。敏捷性可以将结构化的科学思维与非结构化的艺术过程结合在一起。坚定的决心指的是将团队成员的发散思维变成集合思维。团队拥有了坚定的决心,就能把不同的理念和方法都结合起来,形成最佳的解决方案。
3S思考法由批判性思维范围内的系统思维、统计思维和科学思维三个方面组成。
系统思维将价值流分为3个部分。系统指的是相互关联的过程的集合。系统思维就是从整体角度出发来审视所有过程的集合。系统思维是一种有条理、科学、合乎逻辑的逐步思考方法。
统计思维将所有工作都视为一种函数过程“f(x1…xn)”,σ表示偏差,存在于所有过程中,并且意识到对偏差的了解和管理是取得成功的关键。
科学思维是5步流程。这5个步骤需要研究员观察后做出假设,设计并完成实验,然后分析数据印证或推翻假设,在必要的情况下提出并验证新的假设。科学思维可以促进逻辑思维,而不是感性思维。
人力资源方法包含员工招聘、岗位职责培训、就业保障、职业发展路径、团队合作机会、绩效奖金和沟通。关键的人力资源实践其实可以总结为沟通和培训两部分。沟通包括建立开放的对话并形成相互信任和团结协作的文化。培训包括指导员工使用新型工具和流程,并建立一个便于学习和持续改进的环境。最终,从清洁工到公司总裁,所有员工的工作都是“增值和解决问题”。
人类天生就有解决问题的能力。各个团队以及团队合作对于持续改进都很关键。团队成员以及每个团队都有3种解决问题的资源——技能或知识(掌握的知识)、智力水平(每个团队成员的智力)和认知风格(所喜欢的解决问题方式)。
团队成员可以从那些完成过多个持续改进项目的同事那里学习经验。智力代表一个人批判性思考的能力,是否能发现两个学科之间的联系,以及能否在变化的环境中解决问题。认知风格是可以评估出来的,能保证持续改进团队的多样性。
“Kirton适应—创新理论”( Kirton Adaption-Innovation ,简称KAI)可以评估认知风格。一个人在利用自己的技能和智力解决问题时,是采用有创意的方式去调整适应(代表人物:爱迪生)还是用有创意的方法去创新(代表人物:爱因斯坦)?M.J. Kirton博士在1976年提出了KAI理论。KAI分数分布范围从40(适应)到150(创新)(图2)。一个人的KAI得分不受年龄、智商、工作地位、文化和受教育程度的影响。对该理论的应用存在矛盾:我们需要用这个理论来解决问题,但它反过来又会太限制我们。认知团队的多样性能将持续改进的作用和解决方案的效用发挥到极致。一旦形成,多样化团队就能解决各种各样的战略性难题和战术问题。如果想充分利用认知多样性,一定要对其加以指导和质疑。
图2:KAI分数分布
所有的质量管理体系(QMS)都包含持续改进要素。例如,ISO有7条质量管理原则,其中第5条的重点就是持续改进。航空航天(AS)9100质量管理系统是ISO 9001质量管理体系平台的延伸。AS9100采用了过程研究法,并入了“计划—执行—检查—行动”(PDCA)循环和基于风险的思考方式。全面质量管理(TQM)是一种以事实为基础的理念,将质量作为满足客户需求、提高客户满意度的标准。TQM以客户为中心,并通过持续改进来满足客户需求。在20世纪末21世纪初,精益制造和六西格玛理念开始被并入到单一质量管理体系中,叫做精益六西格玛。精益六西格玛的目标是利用精益制造的理念和六西格玛工具加快流程速度、杜绝浪费、减少缺陷和偏差。不论使用什么样的QMS,都可以使用标准的持续改进工具(图3)。
图3:持续改进工具
除了图3列出的9个标准持续改进工具之外,还有4个常见的持续改进活动。将持续改进工具和持续改进活动相结合,可以得到协同效果。持续改进活动包括现场管理(gemba walk)、6S、改善(kaizen)活动和对标。
现场管理是指相关负责人到生产现场视察,确定工艺流程的设计是否能达到原本的目的,以及操作员是否积极达成目标。持续改进团队要通过发现问题所产生的现象去发现可以避免的浪费,而不是直接提出解决方案。这些团队依靠操作员提供宝贵的信息。
5S管理制度起源于日本,是保障工作环境卫生的方法。在现代应用中,单独强调了安全的重要性。6个S分别是:整理(sort)、整顿(straighten)、清扫(shine)、清理(standardize)、素养(sustain)和安全(safety)。6S法可以让任何人看一眼现场就能识别出异常,是持续改进、零缺陷、降低成本和保障安全工作环境的基础。
改善活动是做出调整,以此来影响持续改进活动。“改善”这个理念的发展要归功于丰田汽车公司。改善活动的战术侧重点非常简单,将知识资本置于成本之前优先考虑,寻求的是不太需要动脑子且时间较短(2天~5天)的解决方法。
对标是一种系统化流程,它寻求的是能够实现更优性能的最佳方法、创新理念和高效操作程序。对标活动要么以工艺流程和性能为重点,要么以策略为重点。
工艺流程:致力于确定最高效的运营方法
性能表:价格、技术质量、辅助产品或服务功能、速度、可靠性和其他性能特性
策略:长期有竞争力的模式
对标不同于传统持续改进工具和活动,是一种独特的活动,可在组织内、行业内或者整个行业外进行。
持续改进项目通常会采用、调整所提出的解决方案,或放弃所提出的解决方案:
采用就是接受并实施所提出的整个解决方案
调整就是择优选择所提出方案中的精华部分
放弃就是否定所提出的整个解决方案
理想情况下,持续改进方案是简单、迅速且有效的。最后就到了知识管理发挥作用的时刻了。团队必须要正式记录项目及所收获的经验和知识,应采用A3大小或与之相当的报告格式。
总结
质量和持续改进活动有着悠长的光辉历史。质量不良导致的成本损失和人们对高可靠性的需求,是推动当今时代持续改进的催化剂。持续改进需要不断的变化,组织内的领导和管理层很有必要带头形成一种持续改进的文化。没有配备管理层的领导层只会趋于平庸,而没有领导层的管理层则如同灾难。所有员工必须清楚自己的主要职能就是“增值和解决问题”。质量管理体系(QMS)包含持续改进的要素,共享常用工具和活动。深入了解这些工具和活动并掌握其应用知识至关重要。人力资源是所有资源中最重要的部分,开发人的才能需要放在首位。
参考内容:
- “Theory C: The Near Future of Quality Management,” Kemenade, E. (2014), The TQM Journal, 26(6), 650-657.
- American Society for Quality (n.d.). History of Quality [Quality topics A to Z]. Retrieved from http://asq.org/learn-about-quality/history-of-quality/overview/overview.html.
- Introduction to Statistical Quality Control (7th ed.), Montgomery, D. (2013). Hoboken, NJ: John Wiley & Sons.
- “Forgotten Contributions to Scientific Management: Work and Ideas of Karol Adamiecki,” Debicki, B. (2015), Journal of Management History, 21(1), 40-67.
- The Handbook for Quality Management 2nd Ed., Pyzdek, T. & Keller, P. (2013). United States: McGraw-Hill Companies.
- Get it Right. A Strategic Guide to Quality Systems, Imler, K. (2006). Milwaukie, WI: ASQ Press.
- “Cost of Quality: Not Only Failure Costs,” Buthmann A. (2017). Retrieved from https://www.isixsigma.com/implementation/financial-analysis/cost-quality-not-only-failure-costs.
- Acceptability of Printed Boards (Standard No. IPC-A-600J), Association for Connecting Electronics (2016), Bannockburn, IL: IPC.
- Acceptability of Electronic Assemblies (Standard No. IPC-A-610F), Association for Connecting Electronics (2014), Bannockburn, IL: IPC.
- Collective Genius: The Art and Practice of Leading Innovation, Hill, L., Brandeau, G., Truelove E. and Lineback, K. (2014). Boston, MA: Harvard Business Review Press.
欢迎扫码关注我们的微信公众号
“PCB007中文线上杂志”
点击这里即可获取完整杂志内容。