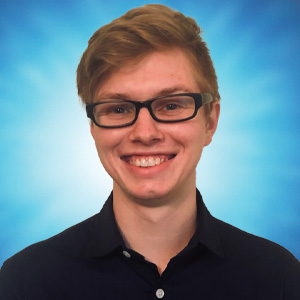
在湿制程中,薄型材料和基板(厚度湿制程中的薄型材料传输具有挑战性,因为要完成传输,传送带需要有开放空间。在PCB制造中,所有湿制程的目标都是让液体与产品表面相互作用。大多数情况下,都是通过喷洒来完成的。如果想从PCB的顶部和底部进行相互作用,那么必须有间隙,让喷雾通过并到达物体表面。如果传送带是一条简单的扁平传送带,可以使PCB平整通过,让产品从传送带的一端到达另一端,但它的底部不会被蚀刻。即使传送带是多孔的,仍然会留下阴影标记,因为在整个过程中,PCB和传送带之间的接触点将保持不变。传送带底部需要有足够的间隙,还需要改变与板接触的位置。这就是为什么目前的湿制程传送带是这样设计的(图1)。
图1:标准湿制程输送带
进行正常的湿制程需要间隙,会造成一些困难。输送带上的任何间隙都为拐角向下倾斜提供了机会。材料越薄,这种情况发生的可能性就越大,尤其是当药水喷到其顶部时。当这种情况发生时,可能会导致边缘或角折叠或“起皱”。这种情况的发生是因为面板各部分的运动不均匀。一旦发生,会降低板的这一部分向前的速度,而板的其余部分在输送带移动时保持一致的向前速度。
引导带方法
尽管这些复杂状况可能是重大障碍,但它们并不能阻止挠性PCB制造商使用湿制程。引导方法已经普遍使用了很多年。有了它,(使用耐化学性胶带)将一块刚性板粘在需要经过湿制程的薄型材料的前缘。这样可确保挠性电路的前缘不会落入间隙中,从而不会形成误差。由于这种下垂问题是薄型材料传输的主要问题,因此该方法倾向于提供一致的结果。尽管如此,大多数挠性电路制造商都希望避免使用引导带,因为施加和移除引导带需要花费人工。这一过程需要时间,而且容易出现人为错误,这会带来面板进一步损坏的可能性。
无引导方法
如果不需要引导带,另一种解决方案必须针对传送带进行设计。通常,解决方案是提供更大的传送带密度,这意味着传送带中的间隙更小,发生错误的可能性更小。主要的缺点是传送带可能会抑制底部的蚀刻速率,因为喷雾更难到达面板。
表面张力是薄型材料无引导传送带来的另一个问题。通常在湿制程设备中,滚筒确保每个湿制程部分的化学药水都包含在其模块内,不会泄漏到其他模块中。有时,对于较薄的材料,面板上的液体会产生足够的表面张力,使面板黏附并包裹在滚筒上。为了避免这种情况,可使用轻型滚筒或减少表面积的滚筒。
结论
如果想放弃使用引导方法,需要了解薄型材料和基板的湿制程,使用专门的设备。虽然专用设备可以帮助传输这些材料,但还不足以保证无错误。尽管存在一些限制,但我预计无引导的薄型材料传输很快就会成为过去式。
更多内容可点击这里查看,文章发表于《PCB007中国线上杂志》23年6月号,更多精彩原创内容,欢迎关注“PCB007中文线上杂志”公众号。