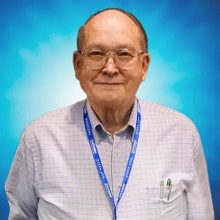
对于PCB制造商,对准是最重要的特色之一,但多层板制造商为达到其对准能力需要做很多工作。CAM设置、多层层压、X射线分析、AOI测量、成像能力以及钻孔精度都会对对准能力产生重要影响。此外,软件和在制板参数附连板也很重要,因为它们有助于提高对准性能。
对准软件
对准软件(图1)给出了CAM工具在底片补偿时用到的数据库和文件,还可以实时校正多层结构移位和钻孔偏差。
图1:用于PCB对准的性能软件可以实现卓越的对准
现代AOI技术、X射线成像技术和物联网传感器(例如共焦成像)都可以连接到对准软件,提供实时在制板测量数据,从而可针对内层偏移计算修改后的最佳钻孔位置,并可将这些变化应用于外层直接成像。这样不仅有助于提高良率,同时还可以提高受控阻抗的精度(可达±3%),详见图2。
图2:对准软件收集和分析各种测量数据,以提升每块生产在制板的性能
其他性能实例
其他对准性能的实例(图3)展示了目前全球最现代、最环保的PCB制造商之一GreenSource Fabrication使用的系统。GreenSource使用的对准和性能软件可以根据生产数据得出经验教训,了解实时发生的情况,并预见到如何通过规范措施来改善WIP性能。
图3:GreenSource Fabrication使用的对准和性能软件
参数化PCB附连板
有一些参数化附连板可以放置在测试板或生产在制板上,为对准软件提供数据。目前可用的参数化附连板有5种,另外还有3种可用作参考和启发灵感:
-
IPC D型附连板
-
CAT 附连板
-
IPC-PCQR²基准在制板
-
HATSTM 和HATS²TM
-
IST附连板
适合自己动手制作的附连板:
-
IBM的CITC附连板
-
PerfecTest 附连板
-
HP的PTS附连板
IPC D型附连板
IPC-2221B附录A中的IPC D型附连板用于对生产在制板上的贯穿孔、盲孔和埋孔进行可靠性测试。它们是两组串联通孔,通过4线开尔文电阻测量来监控电阻。图5g中展示了两个D型附连板。
导体分析测试附连板
导体分析技术(conductor analysis technology,简称CAT)是目前运行时间最长的参数化附连板系统。CAT起源于Sandia National Laboratory实验室的NCMS计划,1994年,创始人Tim Estes和Ron Rhodes从Sandia获得了测试机器的使用许可,创建了CAT测试。测试设备和测试方法已获得了美国专利,专利号为5,659,483。由于这项技术经受住了时间的考验,并且测试方法较为详尽,有大量相关的出版物可以佐证,所以CAT附连板是最常用的基准技术。6个尺寸均为25.4 mm × 25.4 mm(1.0in × 1.0in)的附连板组成CAT主传感器(图4a~f),分别是:
-
导体:间距
-
通孔的形成:网菊花链
-
对准:内层和外层
-
新型对准:内层和外层
-
阻焊层对准
-
阻抗
图4:导体分析技术(Conductor analysis technology,简称CAT):a)导体/间距附连板;b)4通孔-网菊花链附连板;c)对准附连板;d)钻头过冲附连板;e)阻焊对准附连板;f)阻抗附连板g)灵敏的交流斩波4线微欧测试系统;h)采用Agilent34401A测试仪的便携式附连板测试系统;i)交流斩波4线微欧测试系统探针特写;i)4线开尔文测量配置的电流和电压;k)*14层通孔刚性板的剖面图,显示了厚度范围和各种通孔、盲孔、埋孔、亚复合材料和背钻通孔;可用的各种板层、在制板和结构
像CAT这样的参数化系统,其价值在于能够了解工艺、程序、机器和材料的真正能力。每个附连板上有诸多特征,通过调整这些特征,可以捕捉工艺、程序、机器和材料的目前能力。这些特征比较复杂,无法进行检验或分类,只能是真实地反映发生的情况。对于新手用户来说,他们总想通过检验来获得完美的样品。这种操作都是徒劳,因为一些特征在设计时就已经超出了目前的能力。
可以通过CAT定制以下附加板参数:
-
导体间距(1~20 mil)、通孔直径、通孔焊盘、菊花链顺序、层数、对位灵敏度和层数、通孔结构(贯穿孔、盲孔、埋孔、跳孔、堆叠孔、顺序层压等)
-
阻抗类型(单端、差分、边缘耦合、宽边耦合、共面等)
-
整体厚度以及布局,在制板尺寸
可设计去除一些附连板部分,以放入小型测试仪中。
图4g展示了主要设备。该设备由Sandia 设计,由对准系统、固定装置和针床组成,针床连接到灵敏的交流斩波4 线开尔文电阻测量系统(图 4j),该系统再连接到电脑。1999 年,人们设计出一种便携式系统,以便可以使用Agilent 34401A电压表在生产过程中读数(图4h和4i)。该便携式系统有从0.33in×3.0in到0.5in×2.0in的其他附连板,以便于测试生产在制板的布局和自动计算响应的软件。2003年,为了改进阻抗测量,这类设备中又添加了Polar RITS-510机器人探针和测量装置。
IPC-PCQR²基准在制板
图4k展示了14层通孔刚性PCQR² 板的剖面图,显示了厚度范围和各种通孔、盲孔、埋孔、亚复合材料和背钻通孔。如图4i所示,IPC PCQR²程序下有各种板层、在制板和结构可供使用。
HATS和HATS² TM
高加速热冲击 (highly accelerated thermal shock,简称HATS) 技术于2003年开发,HATS²于2020年发布,使用这项技术以后,可以根据IPC-TM-650测试方法2.6.27B、测试方法2.6.7.2c完成高达260℃的多周期对流回流焊仿真,也可以根据其它自定义回流焊温度曲线进行模拟。这种使用高速原位电阻测量的对流回流焊仿真方法可以检测出对流回流焊的高温/膨胀状态下通孔结构中出现的裂纹和分离情况,这些位置可以在较低温度下重新机械连接并且无法检测到。HATS最多可以测试72个IPC-2221B D型附连板(图 5a~g)和36个传统 HATS或带有单个通孔的HATS²附连板,既可以用于多循环对流烤箱回流焊仿真,也可用于55~260℃之间的热冲击/循环(图5c~g)。 HATS²中的7个网是:
-
第1个网:仅第1层和第2层微通孔结构的36个通孔菊花链(整个通孔结构构建在附连板上,但仅测量微通孔结构)
-
第2个和第3个网:仅第1层和第2层微通孔结构的单个通孔(整个通孔结构构建在附连板上,但仅测量微通孔结构)
-
第4个网:测量整个PCB上完整的通孔结构,包括埋孔在内
-
第5个和第6个网:仅第n/n-1层微通孔结构的单个通孔(整个通孔结构构建在附连板上,但仅测量微通孔结构)
-
第7个网:仅第n/n-1层微通孔结构的36个通孔菊花链(整个通孔结构构建在附连板上,但仅测量微通孔结构)
图5:通过以下方式完成高加速热冲击(HATS):a)产生冷却空气和加热空气,使这些空气通过测试夹具,测试夹具含:b)如图所示36个测试附连板;c)1.0in X1.0in附连板;或d)2.0inX1.0in附连板e)0.5inX10in附连板;f)HATS²;gIPC-2221D型附连板
互连应力测试™(IST)
IST是业内最古老且最常用的加速热通孔可靠性系统。该系统由加拿大Digital Equipment公司于1989年开发并在1994年取得专利;1995年,PWB Interconnect Solutions公司完成了这个系统的商业化,并在全球范围内安装了100多套系统。目前有120多家OEM、EMS公司和PCB制造商使用该系统。该公司在全球拥有6个授权服务中心,并通过IPC-TM-650测试方法2.6.26(直流电流感应热循环测试)进行标准化。
图6a展示的常见附连板是OEM为IPC 3级板提供的附连板。该产品具有通孔、盲微孔和埋孔,使用了高Tg、低损耗的层压板。每块线路板都内置了其中两个附连板,并且在通过批准数量的IST循环次数后,才会组装PCB。若出现故障,需找PCB制造商进行分析。
IST方法是在通孔经受热循环时测量通孔和内层连接的电阻变化。热循环是通过在电阻内层上施加高电流而产生,这些内层由一组特定小孔(通常是200个串连的通孔)相连,并且通过两个叫做电源电路的相邻层互连(图6c)。打开电流开关3分钟,产生的热量使连接层从室温升至指定温度。断电后采用强制空气冷却,连接层会在2~3分钟内冷却(图6f)。另一个接受测试的互连结构组是两个独立的菊花链,它们通过各个级别的任意两个内层互连500个通孔,叫做读出电路(图 6b)。图6d中显示了两组互连的等距视图,它们平行运行且按顺序重叠。图6e展示了可以固定试样、提供电流、完成冷却和电阻测量操作的设备。
由于互连结构的热膨胀系数不同,将出现加速失效的情况。失效可能发生在多个位置(图 6g),可能是通孔裂纹、加热后脱落、连接处裂纹,或者在一个或多个区域内的特定位置出现材料分层。达到特定的拒收标准或经过所需的循环次数以后才会停止循环。
图6:互连应力测试(Interconnect stress test,简称IST)是由直流电流引发的热循环测试:a)常见的6in附连板;b)感知电路菊花链;c)当前IST附连板的说明;d)并联和重叠电源和感知电路的等距视图;e)IST电源、数据采集和固定测试设备;f)常见加热-冷却循环;g)热应力互连的失效模式
IBM CITC /PerfecTest® /HP PTS附连板
IBM的电镀贯穿孔可靠性测试使用了自有的电流感应热循环 (Current Induced Thermal Cycle ,简称CITC)PCB附连板。该单网小附连板由IBM根据IPC-TM-650 2.6.26测试方法B设计,上面包含了100 个通孔,尺寸仅为1.75in×0.3in,可在在制板上多次使用,并可轻松适应在线工艺监控。该测试用施加电流的方式以每秒3℃的速度将附连板加热至245℃,停留时间为40秒,每天重复该循环200~700次。会连续测量电阻温度系数 (Temperature Coefficient of Resistance,简称TCR)并用于确定附连板的温度。4线电阻电桥可监控通孔菊花链。附连板如图7所示。
CITC循环经过了FEA建模、TMA和莫尔条纹验证,并已被IBM使用了30年。这项测试速度很快,附连板尺寸也非常小,正是有这项测试,IBM和I3公司才能够表征PCB制造过程中的许多重要步骤。
PerfectTest于1989年问世,旨在解决多层材料移动和钻孔对准问题。附连板(图7a、7b)被放置在多层在制板的外边缘,其工作原理是检测哪些电镀贯穿孔已检测到特定内层铜楔的移动。图7b说明了附连板在X-Y轴上将以0.002英寸增量检测到从1~9mil的移动。附连板可以放置在每一层或仅放置在特定层上。虽然不需要特定的测试设备,但图7c中展示的PerfecTest 设备还是配备了分析和数据存储软件。
图7:a)PerfecTest是测试材料移动及对准的附连板系统。附连板尺寸为0.2inx1.73in,放置在多层在制板的边缘;b)PerfectTest的工作原理;c)测试设备探针头。HP设计的7个附连板(PTS):a)外层对准,增量为0.00025英寸;b)内层对准和偏移增量为0.00025in,包括 0.1mil X射线游标;c)多层上的走线/走线/焊盘开路和短路;d)电镀贯穿孔连续性图形,包括与PTH形成不同角度的内层外层连接;e)对0.00025in的底片缺陷分析;f)对0.00025in增量的蚀刻因子分析。A)HP配有连续性测试仪的PTS布置;B)针对单个附连板的测试夹具;C)在开尔文4线测试结构中使用1安培电源和数字面板表进行毫欧级测量
PerfecTest虽然已经在2013年关闭,但全球各地的许多公司仍在继续使用他们的附连板。可以使用简单的ET连通性测试仪或自制的4线开尔文探针来测试蚀刻后的在制板。
1987年,惠普的印制电路部门根据其公司自1972年以来一直使用的早期附连板,创建了PTS参数化测试系统。这是根据惠普在晶圆制造中使用的参数晶片设计的。这些早期附连板侧重于内层偏移,通过测试内层上铜和电镀贯穿孔之间的短路、莫尔条纹图形和孔质量剖面来得出结论。1983 年左右,中国台湾地区第一家NanYa PCB工厂将参数化PCB用作培训和工艺载体,这对参数化测试附连板的发展产生了影响。这块PCB采用了不同设计规则的技术,并可针对如何改进工艺给出反馈。
HP PTS共有1组7个附连板,可以放置在生产在制板上或在参数化在制板上使用,从而可快速了解工艺的基准能力。最初的7个附连板(图 7a-f)旨在测试:
-
外层对准
-
内层对准和偏移
-
导体/焊盘开路及短路
-
电镀通孔,内层导体连通性
-
底片缺陷
-
阻焊层对准
-
蚀刻因子
工厂的连通性测试仪使用针床开路/短路测试设备即可测试这些附连板。在这种情况下,测试仪为ATG200栅格测试仪。HP工作站可以获取并存储测试仪的故障文件。每个附连板都存储了与故障文件对应的完美响应或网表,将开路和短路转换为尺寸偏移或其他参数数据。RS/1统计程序用于生成控制图、统计报告以及历史数据。
该系统如图7a所示。图7b~c还展示了小型独立附连板测试仪,操作员必须立即检查流程得出信心指数。这些自制的毫欧表与简单的1安培电源适配器、4位数数字面板表和加工过的有机玻璃附连板支架配合使用,该有机玻璃附连板支架配备8个装有弹簧的金针,连接到4线开尔文测量方案中的4位旋转开关中。
这一概念被富士康内部PCB制造团队采用,作为其在中国16家大型PCB工厂的基准测试方法;附连板的类型扩大到了24个,其中许多在测量后会用于组装性能基准测试。
如有需要,可向作者索取这7个附连板的Gerber文件。
总结
自从有印制电路制造业以来,就一直用附连板测试每一个因素。多年来,人们设计了许多极佳的附连板,多到我无法在本文中一一介绍。现在可供选择使用的附连板类型比以往任何时候都多。希望你也正在使用其中的某个系统。可以通过购买、租赁和自主研发的方式得到这样的系统。竞争带来了经济压力,导致附连板系统变得越来越重要。如果没有掌握这项技术,就会发现无论是因为盈利能力还是可靠性,经营都会变得越来越难。