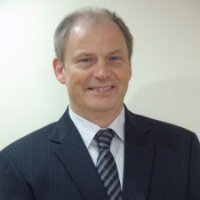
最近所有电子制造中的创新,包括工业4.0,制造互联网,智能工厂,数字制造等,都为工厂运营的许多方面带来了数字化方法。 它们的名字并不重要,因为大多数人对这些东西的理解仍然不同。 然而,实施这些创新的疑虑包括信息传输的兼容性,这一点我们在本系列的第一部分(点此阅读)中进行了讨论,以及我们在第二部分(点此阅读)中讨论的实际的智能应用例子,以及对开放信息平台的需求,这一点能够由诸如开放制造语言(OML)的技术来实现。
数字化数据捕获为创新带来了另一种可能性:运营的完全可追溯性。 现在,终于有了IPC-1782这个专用标准来定义电子设备的可追溯性,该标准的设计目的是提供适当水平的可追溯性,而不会增加任何成本——即以智能的方式。
可追溯性就像监控摄像机一样,监视制造过程并记录下所发生的一切。 如果在生产的任何方面检测到缺陷,则可以通过“慢动作回放”,准确地识别发生了什么。 摄像机可以看到非常多正在发生的不同的事情,因为其具有能够覆盖整个工厂运营的视点。 完全可追溯性不是从单一角度出发的,例如仅从SMT机器获得的数据。 完全可追溯性的优点是能够收集大数据,即来自制造所有不同方面的数据,然后通过分析这些信息来了解不同工艺、事件和动作的相互作用。
我们以SMT贴片机为例,监控可以看到元件贴装到PCB上的过程。 在这个过程中,SMT机会提供这些操作的数据记录,因为机器遵循给出的工程信息。 然而,输出的数据是与送料器的位置相关联的,每个贴装到PCB上的元件都是从送料器上获取材料。 工程数据用一个零件号来标识每个送料器的位置,因此这些数据看起来像是在报告零件号,而不是每个PCB上的参考位置。
然而,这是假设了在该供料器位置设置了正确零件号的情况下。还需要检查材料验证记录来确保设置正确。设置验证可以由机器软件或第三方软件来完成。 为了完全可追溯性,我们需要倒带,来查看与验证相关的实际事件。
首先,材料卷会被装载到进料器上。通常进给器和材料二者上的条形码都会被读取来进行验证,以将两者关联起来。 材料条形码应该能提供零件号,再根据机器的工程信息检查预期使用的位置。 假设该过程正确进行,则可以给机器装载给料器,之后就是对材料已被装载在正确位置的简单自动确认。
然而,即使这样做了,还是有可能会出现问题。 用于验证的零件号要么是通用的“内部”零件号,要么是材料供应商的零件号。 后一种情况会比较难以管理,因为目前来自各个不同供应商的材料标签并不会非常标准化。 验证软件必须“学习”标签格式和内容,如果在材料准备阶段“即时”完成可能会导致严重的问题。 众所周知,条形码标签不可靠,而且不同材料供应商之间,标签也可能发生冲突。
更好的方法是在材料进入工厂或SMT仓库区域时,对每种不同的材料按照独立的零件号进行标记。当这项工作完成后,我们可以通过查看记录确定这些事件,从而达到更好的可追溯性。 当材料进入时,读取供应商条形码,并且进行通用内部零件号转换。 最常见的情况是,使用相同的通用零件号的材料有可能是来自两个或更多供应商的。这些将在机器上使用的材料的形状、尺寸、方向、甚至封装方式都有可能是不同的。
简单地使用内部零件号标记材料意味着在材料被装上机器之前无法发现这些差异,如果你足够幸运的话。 验证流程不会记录下任何问题,但如果没有发现这些差异的话,可能会造成机器异常,包括出现大量缺陷。 所以,可以使用材料的唯一识别编码来存储包括零件号以及其他可能会对操作出现重大影响的材料的所有其他信息来记录,包括物理差异,供应商特定单位以及诸如湿度敏感设备(MSD)等参数。 通过以这种方式为每种材料存储唯一的配置文件,验证过程就能变得更加可靠并且减少材料补充过程中的变化,因为当需要补充材料时会自动选择对应供应商的材料。
机器自带的简单验证软件可能无法满足更高级检查的要求,除非它能够理解每种材料的完整配置文件。 因此,机器软件需要与工厂的物料管理软件相连接。 工厂级的智能和精益材料管理功能也可以利用机器数据,提供相互操作的价值。
这一系列过程都由我们的可追溯性摄像机记录下来。 只是检查零件号是否正确,就能够满足基础级别的可追溯性。 另一方面,大多数知名电子制造商需要对质量和责任进行明确的控制,所以需要更高水平的可追溯性,其能够涉及到工厂内不同系统之间的切换的细节。
这个SMT材料可追溯性的简单例子表明,整个解决方案不能完全来自一个点,需要进行自动协作。 许多其他流程都会消耗材料,包括手工装配和维修,以及诸如MAC地址的虚拟材料的配置。 还存在诸如焊膏的可消耗材料,其本身就需要遵循的复杂工作程序,所以使用了类似的不同等级可追溯性数据采集。
然而,可追溯性并不止于只针对简单的材料。 通常,子组件被用作产品组装过程中的零件使用,而其需要从生产历史中继承其可追溯性数据。 装配操作的记录必须与在不同时间和不同位置进行的其他记录相关联,但是它们需要完全兼容,以创建成品的完整记录。
可追溯性涵盖的不仅仅是材料。 工艺历史也是制造记录中的关键部分。 智能工厂系统不断对工厂运作进行计划,确定最佳的产品流程和最佳的机器配置设置。与产品的每个工单相关的信息,包括工艺设置配置,也要通过我们的可追溯性摄像机记录下来。 这一环的规划信息是至关重要的,因为我们需要确保所有的工艺在正确的条件下按正确的顺序设置和执行,并且工艺的结果良好。
尤其是测试过程,其能够提供关于每个产品的大量数据,以及简单的合格或不合格结果。 未通过测试的产品必须送至维修站。 这些过程也需要与可追溯性数据直接交互,以确定在可追溯性数据记录中,也就是整个生产周期记录中的偏差是否有可能会造成问题的原因。 一旦发现缺陷,就触发了对是否需要对该工艺采取纠正措施的评估,或是否需要对先前完成生产的产品进行再次检查的评估。
在这个对工厂运营进行剖析的简单例子中,我们可以看到需要从生产的所有方面交换数据:直接、间接和事务。 直接从工艺收集的数据仅在之前采用的工艺以及事务活动通过验证的情况下才有效,在这个过程中,通过了机器的材料,PCB以及操作达到该时间点。 机器数据的重要性在于,其允许我们的可追溯性摄像机观察操作的进度,建立可以与其他所有方面对相应的时间线,以便在记录中进行回放。
关于IPC-1782
IPC-1782 [1]电子产品可追溯性标准是一个用于获取材料和工艺数据的综合标准,其中定义了4个等级的细节和标准。 了解可追溯性要求对于达到期望的效果至关重要,特别是当需要可追溯性数据来确定复杂问题的原因或确定问题的确切范围时。 标准中明确的定义还意味着仅捕获必要的数据,从而降低成本。
关于OML
OML [2]标准的设计目的是使用单一语言定义实现所有机器和工艺的互连,包括车间的事务活动。 OML支持所有形式的智能工厂活动,能够用于任何数字工厂和工业4.0解决方案,以及作为所有级别的可追溯数据的渠道。 每个机器和工艺只是数据收集的一个点。 OML允许多个不同的智能应用同时使用该数据。
智能可追溯性
使用以自动方式获取的工艺数据流能提供满足几乎所有要求和等级的可追溯性数据。 它类似于来自摄像机的视频信号,包括画面中的每个方面。 这意味着可追溯性的成本实际上有可能变成负数。 不同于通过额外的操作来收集,筛选以及存档可追溯性数据,本文所描述的整个过程能够通过与智能工厂运营协同的方式来自动化进行。 拥有所有事件的“视频”记录,能够发掘出可追溯性数据的全部潜力,这带来了最高级别的主动质量管理的机会,以及对可能发生的任何问题的完全控制。 将智能技术中的这些元素结合在一起,无论优先级或方法如何,通用的智能工厂或数字工厂平台能够有效地将所有这些元素结合在一起,实现IPC-1782定义的全面可追溯性。
参考文献
- IPC 1782 can be purchased by clicking here.
- The OML Community website is at www.omlcommunity.com.